The main purpose of welding process evaluation is to prove whether a certain welding process can obtain the welding joint that meets the requirements, so as to judge the correctness and feasibility of the process, rather than to evaluate the skill level of the welding operator.Welding process evaluation is an important prerequisite to ensure the manufacturing quality of welded structures.
This paper mainly compares the differences of mechanical properties test methods of butt welded joints (butt joints for short), including differences in sampling, differences in mechanical properties test content and differences in evaluation basis, etc., for reference of relevant test personnel.
Procedure for welding procedure qualification
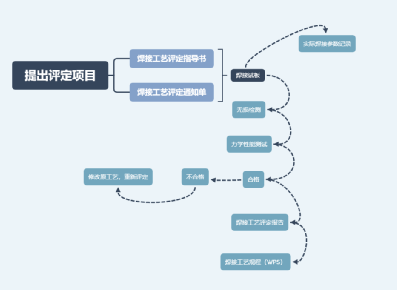
Welding process evaluation requires skilled welding personnel.The WPS report does not directly guide the production, but is the supporting document of the WPS. A WPS without the support of one or more WPS reports is meaningless.The welding process qualification procedure is shown in Figure 1.
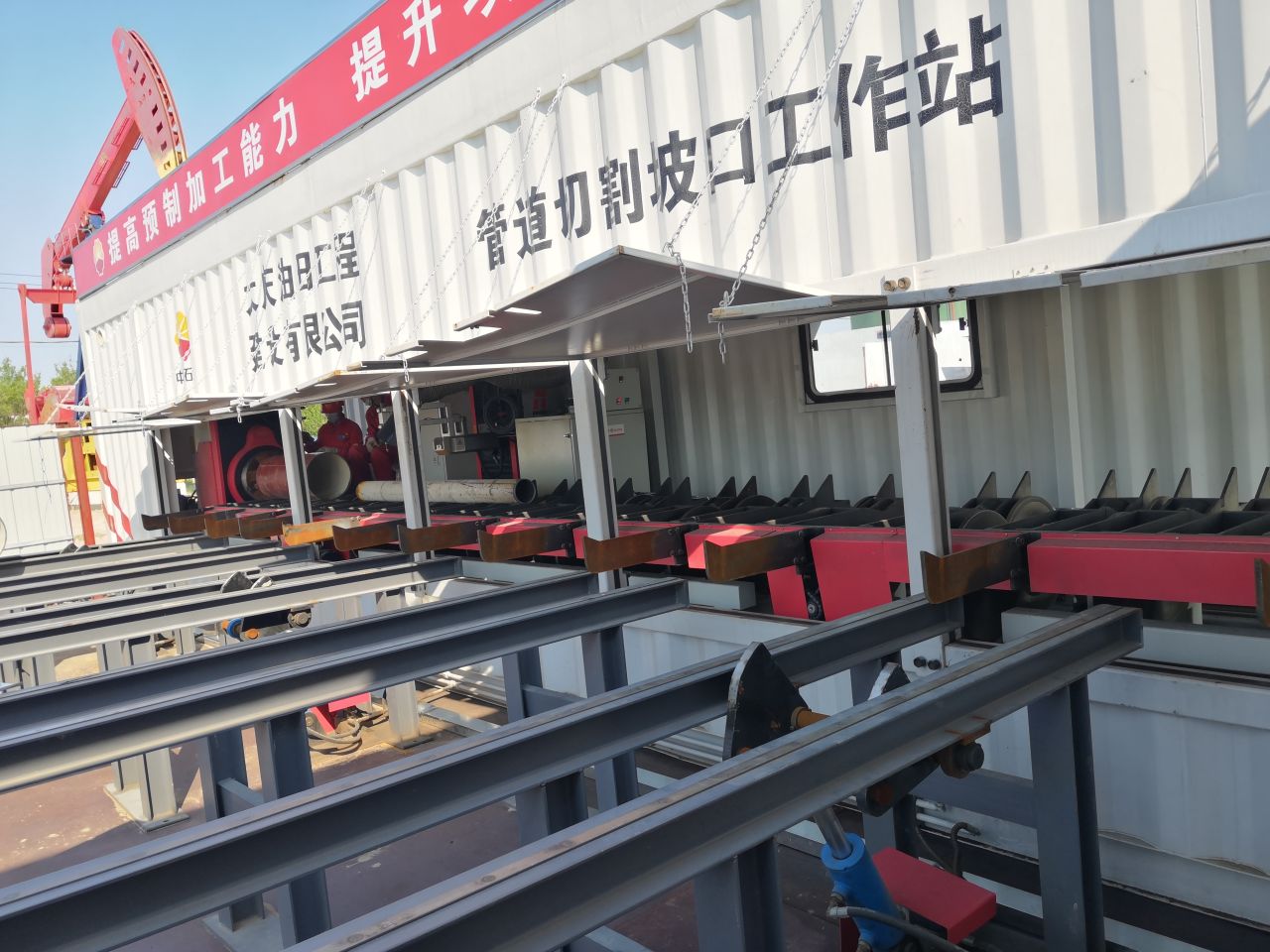
Welding process evaluation test through the tensile, bending, impact and other mechanical properties of the weld joint test, to know the quality of metal material weldability, metal welding process is simple and the joint quality is high, good performance is called good weldability, on the contrary, it is called poor weldability.
In the welding process evaluation, stretching and bending are necessary items, but for the impact test is not all required, generally carbon steel is required to do, stainless steel is generally not required to do impact, unless the design requirements.The first difference is the minimum plate thickness specified in the selection of side bending specimens.
The special one is NB/T 47014-2011. Although side bending test is carried out when the thickness is greater than or equal to 20mm, it is also stated that side bending can be used instead of face bending and back bending when the thickness is greater than or equal to 10mm. In particular, side bending should be used when the welding seam is combined with different welding methods.Second is the hardness test, EN ISO 15614-1:2004 +A2:2012 in addition to the yield strength is less than 275MPa of carbon steel, austenitic stainless steel and nickel-based alloy are required to carry out hardness test, other standards are stipulated according to the actual situation of the project to determine whether the need for hardness test.