During welding, the wire feeding machine often appears the phenomenon of unsmooth and uneven wire feeding, which will bring difficulties to welding and directly affect the welding quality. The welding seam that should be welded at a time is often divided into several sections to be welded, forming more joints, and even affecting the mechanical properties of the welding seam.
Analysis of wire feeding problems in welding:
1. Hard bending of welding wire
2. Rust of the welding wire
3. Uneven thickness of welding wire
4. Improper use of pressing wheel of wire feeder
5. The bending of welding torch is too large when used
6. Grooves are ground in the wire feeding hose of welding gun
7. The conductive mouth is not cleaned in time
8. Excessive wear of wire feed hole of conductive nozzle
9. Current and voltage mismatch during welding
1. Hard bending of welding wire
The welding wire will not produce hard bending in production, but the welding wire of the welding wire tray will be knocked down in the process of handling, or the scattered welding wire will be wrapped to the welding wire tray will produce this phenomenon.
How to avoid
When opening the packaging and installing the welding wire, we should carefully check the welding wire plate to make sure that the welding wire plate is intact and the welding wire is wrapped neatly before it can be used.When handling the wire, we must be careful to handle it, to avoid breaking the wire plate, causing the wire to scatter. When the scattered wire is rewrapped to the wire plate, we should take gloves to carefully wind, to avoid hard bending.
2. Rust of the welding wire
reason
During the transportation of the wire, the packaging is damaged, the wire library is too damp, the humidity exceeds the standard, the storage time is too long, and the wire is stored after being touched by hands.
How to avoid
When opening the packaging of the welding wire, check whether the welding wire is rusty. The rusty welding wire should be replaced in time to the welding wire library.Welding wire packaging shall not be damaged, control the humidity of the welding wire library, the storage of the welding wire should be 300mm away from the ground and the wall, do the first purchase of the welding wire first use, open the use of the welding wire strictly touch by hand.
3. Uneven thickness of welding wire
reason
Production of welding wire due to wire drawing equipment is not qualified.
If the intermittent welding phenomenon will occur after replacing the new conductive nozzle, it must be the uneven diameter of the welding wire should be replaced.
4. Improper use of pressing wheel of wire feeder
reason
Wire feeding machine pressing wheel should be used to match the welding wire, solid carbon steel wire using steel wheel, flux cored wire using ceramic wheel, and the wheel groove model and the diameter of the welding wire match.The pressure shall be adjusted according to the requirements of use, and shall not be too loose or too tight.
How to avoid
According to the requirements of the use of steel or ceramic wire feeding wheel, wire feeding wheel groove model and the diameter of the welding wire to match the wire feeding wheel pressure to moderate, wire feeding wheel groove to often clean.
5. The bending of welding torch is too large when used
reason
Excessive bending of welding gun due to arbitrary welding or the spatial position of special weld.
How to avoid
When welding, the welding gun should be kept straight or bent as far as possible to reduce the running resistance of the welding wire in the wire feeding hose.
6. Grooves are ground in the wire feeding hose of welding gun
reason
Welding gun wire feeding spring hose use time is too long, the welding wire through the wire feeding hose will grind out the groove inside the hose.
How to avoid
When the welding wire enters the grooves ground in the hose of the wire feeding spring, the phenomenon of wire clamping in the grooves will be caused when the bending degree of the welding gun changes, which hinders the normal operation of the wire feeding.When the wire feeding spring hose is used for a long time, the wire is not smooth, and the wire feeding hose after the welding gun hand shakes or blockages with the welding gun Angle change, the wire feeding spring hose should be replaced in time.Keep the welding gun bending Angle as far as possible to reduce the friction of the welding wire in the wire feeding hose.The wire feeding spring hose is too short in the welding torch, which will cause the welding wire to bend inside the welding torch, forming the wire feeding is not smooth.If the wire feeding spring hose is too long inside the welding torch, it will bend, which will increase the friction resistance of wire feeding and cause wire feeding instability.
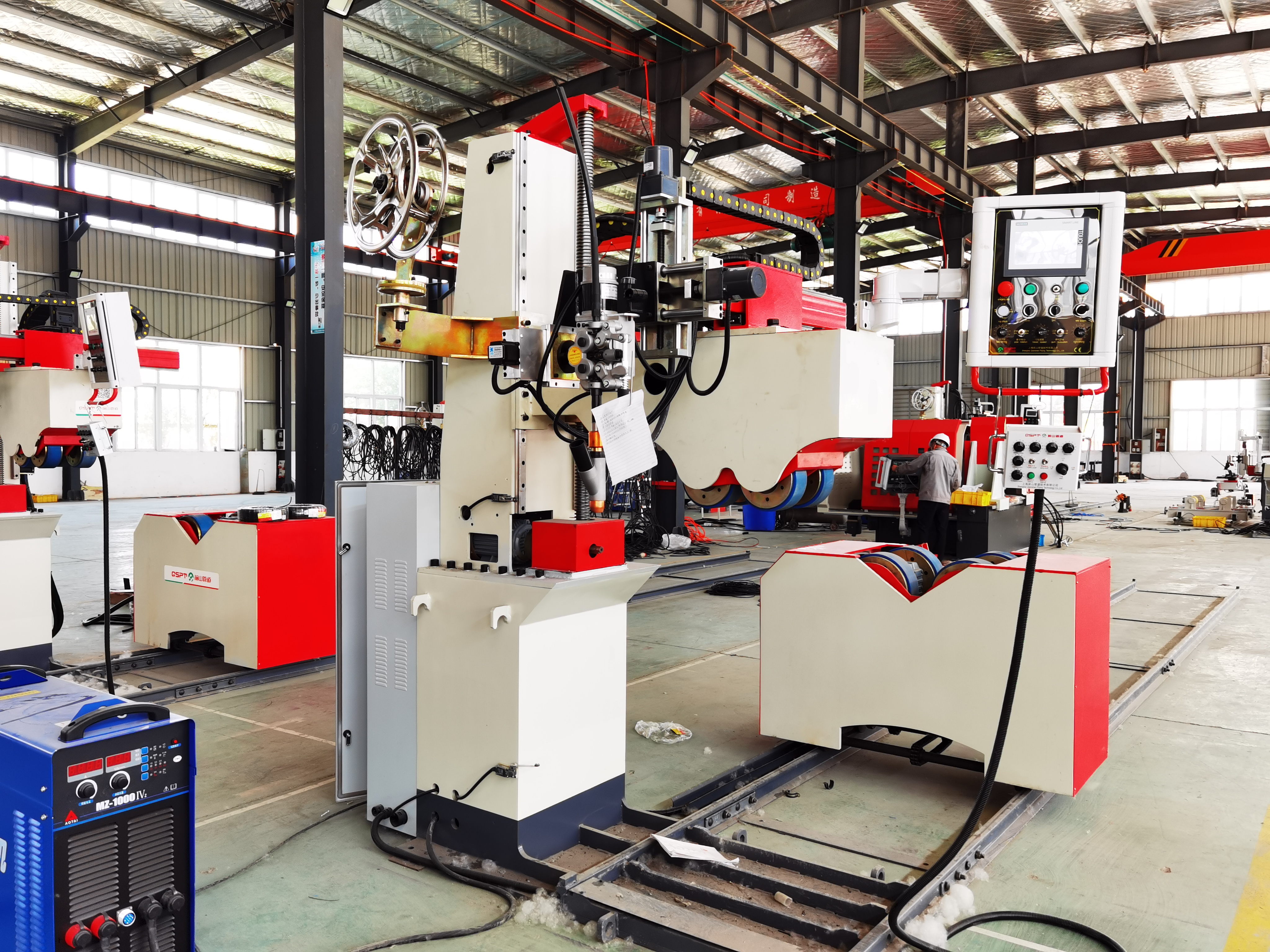
7. The conductive mouth is not cleaned in time
reason
When the welding specifications are not adjusted properly, or the welding gun is too close to the weld pool, the longer the welding time is, the more the welding splashes are adhered to the conductive mouth.
How to avoid
When welding the adjusted the Angle and the welding torch welding wire according to the requirement of tensile length with less spatter, do it often with long nose pliers cleaning splash of conductive mouth, after the clean up will wire out conductive mouth 10 ~ 15 cm long, with the long nose pliers wire from conductive mouth after the root bending clockwise or counterclockwise rapid loosening after 3 to 5 laps, with wire rotary strength of conductive mouthThe wire feed hole is smooth and smooth.
8. Excessive wear of wire feed hole of conductive nozzle
reason
The wire feed hole will be too large if the conductive tip is worn for a long time during welding.
How to avoid
When welding, it is found that the welding wire swings back out of the conductive nozzle and is accompanied by adhesion with the conductive nozzle, a new conductive nozzle should be replaced in time.The conductive nozzle of the welding gun should be matched with the diameter of the welding wire. The diameter of the conductive nozzle hole is too small, resulting in too much friction resistance, so that the welding wire is not smooth or wire blocking phenomenon. The conductive nozzle will cause the welding wire to swing back and forth in the molten pool and make the weld forming bad.
9. Current and voltage mismatch during welding
reason
Insufficient experience in welding without adjustment to specified welding specifications.
How to avoid
According to the production needs, according to the welding specification to adjust, so that the welding wire into the molten pool in time to melt, the sound of the welding wire to the molten pool is uniform.