There are some welding novice or just bought a new welding machine welding friends will appear on some problems, are generally welding failure, but in fact, many times is not to say that the welding experience or welding machine problem, may not be careful enough.Today, I will summarize several problems that are easy to ignore when welding. Pay attention to these problems. There is no problem in welding.
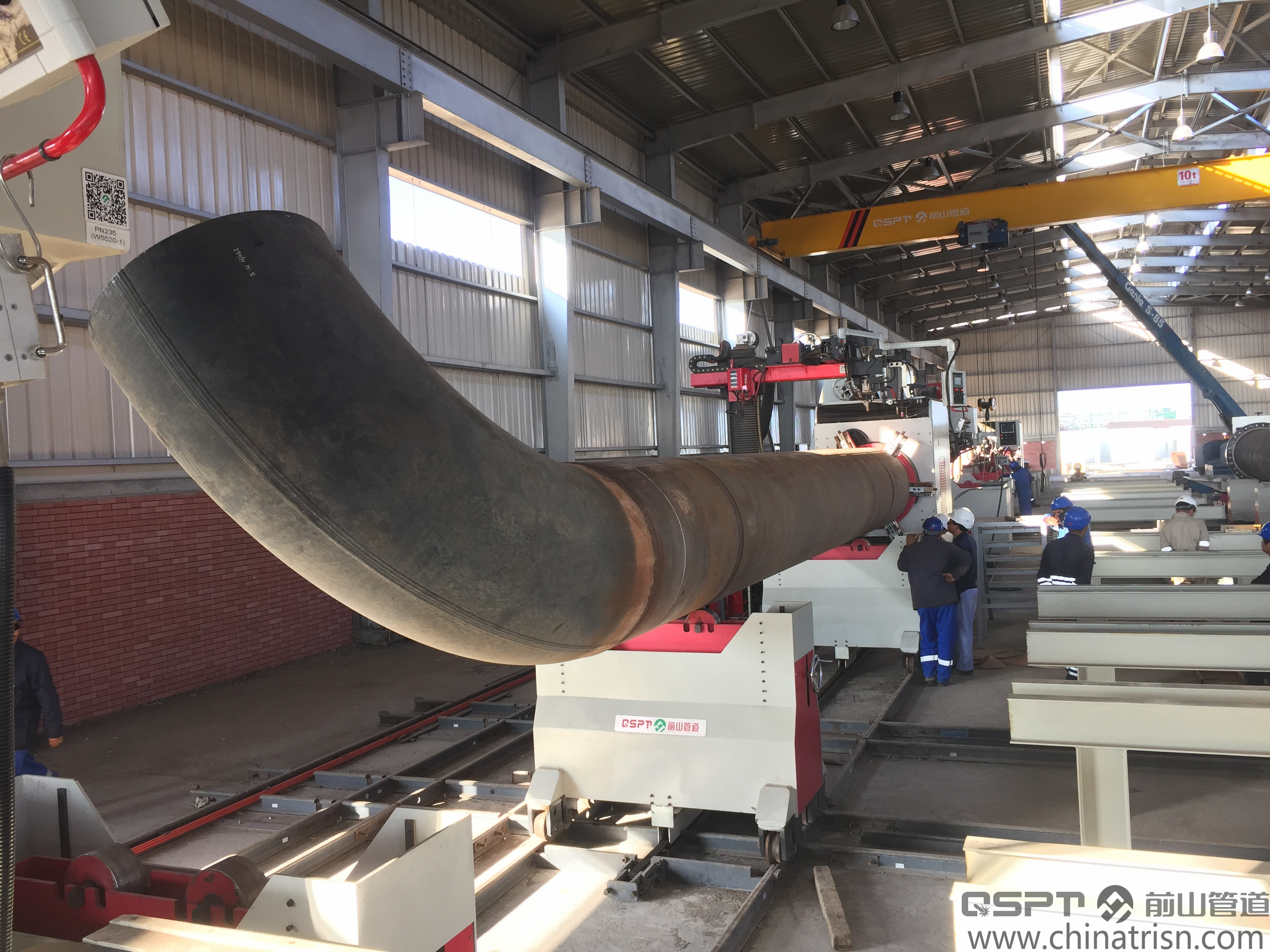
The optimal voltage is not selected for welding construction
[Phenomenon] When welding, the same arc voltage is selected regardless of the size of groove, whether it is backing, filling or covering surface.This may not reach the required depth, width, bite edge, air hole, splash and other welding defects.
【 Measures 】 In general, the corresponding long arc or short arc should be selected for different situations to obtain better welding quality and working efficiency.
2 Welding does not control welding current
[Phenomenon] When welding, in order to seize the progress, no groove is used for the butt weld of medium and thick plate.The strength index declines, or even fails to meet the standard requirements, and cracks appear in the bending test, which will make the weld joint performance can not be guaranteed and pose potential hazards to the structural safety.
[Measures] Welding shall be controlled according to the welding current in the process evaluation, allowing 10-15% float, and the size of the blunt edge of the groove shall not exceed 6mm.When the thickness of the plate exceeds 6mm, the groove shall be opened for welding.
3.Welding speed and welding current, welding rod diameter to coordinate use
[Phenomenon] When welding, the welding speed and welding current are not controlled. The diameter of electrode and welding position are used in coordination.
[measures] welding speed has a significant effect on the quality and production efficiency of welding, choose the fit welding current and weld position (backing welding, filling welding, cosmetic welding), thickness of weld and groove size to choose the proper welding speed on penetration, gas, welding slag discharge, don't burn through, under the premise of forming good choose larger welding speed, in order to improve the productivity efficiency.
4.The arc length was not controlled during welding
[Phenomenon] The arc length is not properly adjusted according to groove form, welding layer number, welding form and electrode type during welding.Due to improper use of welding arc length, it is difficult to obtain high quality weld.
"Measures" in order to ensure the weld quality, more commonly used when welds short arc operation, but can choose appropriate arc length according to different situations in order to obtain the optimal welding quality, such as V groove butt, Angle of the first layer should use the shorter arc, so as to ensure the weld penetration, and don't bite edges occur, the second layer can be slightly longer, to fill the weld.When the weld gap is small, short arc should be used. When the gap is large, the arc can be slightly longer and the welding speed can be accelerated
5 welding does not pay attention to control welding deformation
[Phenomenon] When welding, we do not pay attention to control deformation from welding sequence, personnel arrangement, groove form, welding specification selection and operation method, etc., which leads to large deformation after welding, difficult correction and increased costs. Especially for thick plates and large workpieces, it is difficult to correct, and mechanical correction is easy to cause cracks or layered tears.The flame correction cost is high and the operation is not easy to cause overheating of the workpiece.
[Measures] Adopt reasonable welding sequence and choose appropriate welding specifications and operation methods, and adopt anti-deformation and rigid fixing measures.
6.Multi-layer welding discontinuous welding, do not pay attention to control the temperature between layers
[Phenomenon] When multi-layer welding of thick plate, the temperature control between layers is not paid attention to. If the interval between layers is too long, the welding is easy to produce cold cracks between layers without re-preheating.If the interval is too short and the temperature between layers is too high (more than 900℃), the performance of the weld and the heat affected zone will also be affected, resulting in coarse grain, resulting in decreased toughness and plasticity, and leaving potential hidden trouble for the joint.
[Measures] When multi-layer welding of thick plate, the temperature control between layers should be strengthened. In the continuous welding process, the temperature of the base metal should be checked to make the temperature between layers consistent with the preheating temperature as far as possible, and the maximum temperature between layers should also be controlled.